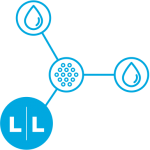
LIQUID | LIQUID
Strata | Liquid-Liquid Separation Vessel
Description
Process complications caused by emulsions can include equipment fouling, off-spec product, increased operating costs, and unscheduled shutdowns which can lead to loss of production and revenue. FTC has the technical expertise required to provide a cost-effective solution to these liquid contaminant issues. Our Strata Liquid-Liquid Separation technology offers a complete line of coalescing and vessel configurations to address even the most complex emulsions. Strata coalescing systems provide excellent coalescing efficiency, capacity, and liquid contaminant removal to improve the overall performance of the process and ensure process reliability.
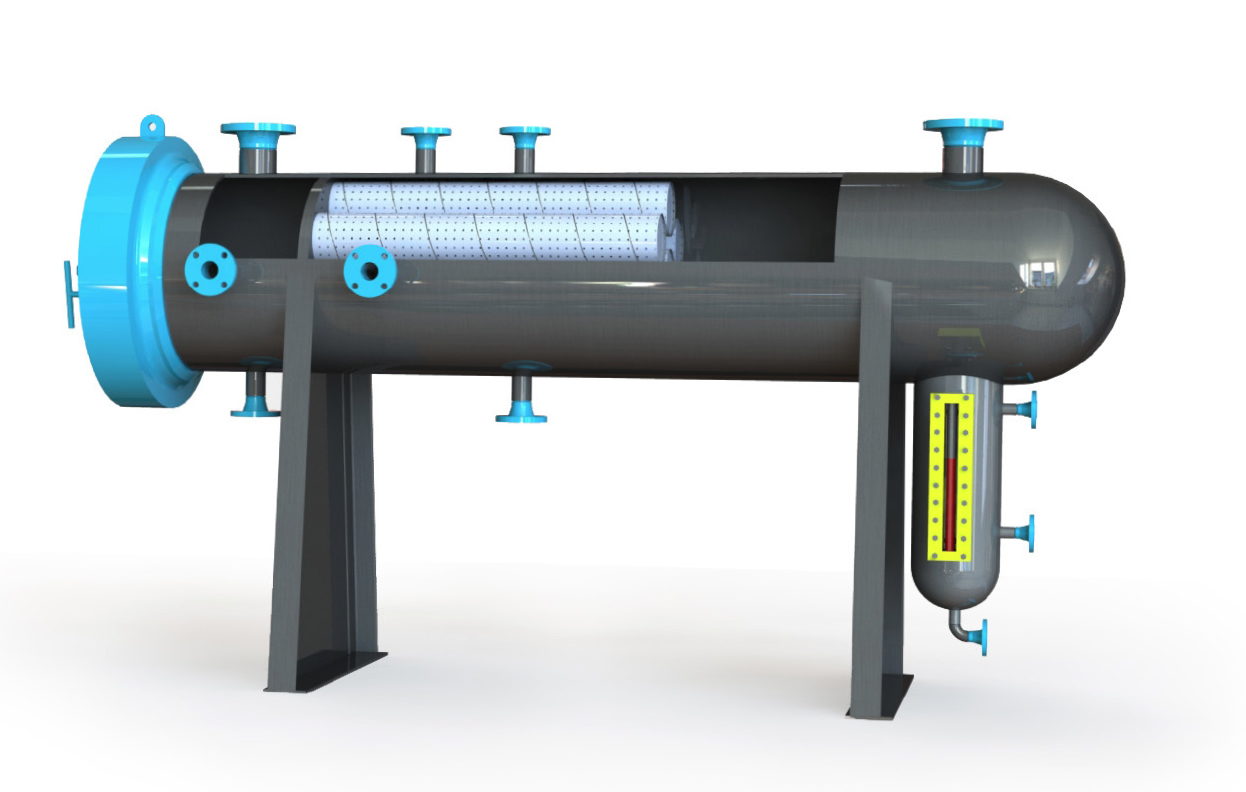
Engineering the Right Solution
Properly designed liquid-liquid coalescing systems efficiently separate the emulsifed or dispersed liquid from the continuous phase of the process stream so that downstream contamination is avoided. Simplifying the system, an emulsion enters a coalescing unit, the fluid mixture passes through the separation medium in an inside-to-outside flow pattern and the small dispersed liquid droplets form larger droplets, or coalesce, and subsequently separate from the continuous phase. The continuous phase exits through its designated outlet and the discontinuous phase is drained from a sump. However, the process isn’t quite so simple; it is actually a complex process with many factors to consider. Creating a system for efficient separation requires technical expertise acquired from years of experience and an expert understanding of the science and parameters affecting the process. Fluid compatibility, viscosity, interfacial tension, specific gravity, and flow rate are all important parameters in sizing an efficient system. In addition, coalescer protection, element design and vessel design are very critical.
Protecting the Coalescers: To operate at their highest efficiency, coalescers must be free from solid contaminants. Installing the correct pre-filtration system upstream of the coalescing unit is critical for proper functioning and operating efficiency. Solid contaminants can plug coalescer media which can lead to more frequent changeouts and less efficient performance. FTC offers a full line of liquid/solid filters and vessels to protect our Strata separation technology.
Coalescer Element Design: The actual coalescence of the dispersed droplets occurs inside the coalescing elements through a 3-step process. First, the process is initiated with the interception of the dispersed liquid droplets in the stream by the microfiber matrix. Next, after the interception phase, the small droplets effectively coalesce within the fiber matrix to form larger droplets. Finally, in the drainage phase, the large liquid droplets are released from the coalescing element. FTC’s engineers understand the science behind this complex three stage process and carefully select the proper element style, media type and layering for each application.
Vessel Design: The separation process is not completed when the droplets leave the coalescing element. The larger droplets exiting the coalescer elements enter the disengagement phase where they separate from the continuous phase more rapidly due to droplet size and gravitational forces. Vessel design is critical in order to provide efficient separation of the discontinuous phase from the continuous phase. Improper vessel design will compromise the separation efficiency and allow the liquid contaminant to exit the vessel with the continuous phase causing contaminant carry over. FTC engineers evaluate the critical parameters of each application such as exit velocities, droplet rise or fall rates, and nozzle locations to ensure proper removal of the discontinuous phase.
Features & Benefits
- High efficiency liquid-liquid coalescence technology provides reliable discontinuous liquid contaminant removal of up to 5% by volume
- Capable of reducing discontinuous liquid phase concentration down to 15 ppmv or less
- Designed to maximum liquid flow and discontinuous liquid phase removal capacity in a minimal footprint
- Engineered to minimize pressure drop and service life
- Offered with a wide range of materials of construction to provide the most cost-effective solution for each application
- Operator friendly designs to minimize capital and operating expenses
Options
- Designed to ASME Section VIII, Div 1; also CRN available
- Horizontal orientation (standard)
- Carbon Steel standard construction; others available
- External paint standard
- Buna, Viton®, and Spiral Wound seals; others available
- Quick Opening, Blind Flanged & Swing Bolt closures;Â others available
- Vent, drain and pressure ports included
- Discontinuous phase drainage sump with ports included
Common Applications
- Water removal from refined products (e.g. diesel, gasoline, kerosene, LPG, etc)
- Water removal from hydrocarbon condensates
- Water removal from LPG and NGL
- Water removal from chemicals
- Oil removal/recovery from water streams
- Amine removal from hydrocarbons
- Caustic removal from fuels
- Hydrocarbon removal from quench water
Markets
- Oil & Gas
- Power Generation
- Chemical Production
- General Industrial
Strata Coalescer Series Available
- Strata 37
- Strata 60
CONTACT US TODAY FOR ADDITIONAL INFORMATION
Call 1.888.436.0849 or fill out the form.