Oil & Gas – Filters, Filtration & Separation Solutions
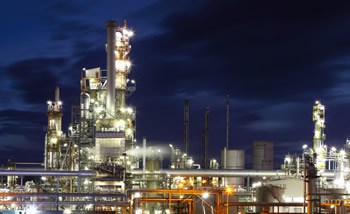
Filtration Technology Corporation has over 30 years of experience serving the oil and gas industry from its offices in Houston, TX. FTC provides filtration and separation solutions for the production, transportation and purification of hydrocarbons and associated fluids and gas. Our filter and separation productions combine absolute-rated performance technology with long service life, enhanced productivity, and cost savings to all segments of the energy sector. Included in these markets are the following:
Completion Fluids
FTC has extensive experience in the filtration of completion fluids. We understand the degree of filtration required during well completions to properly protect the formation and prepare the wellhead for production or injection.
Produced Water
FTC has expertise in preparing water/brine either from wellhead discharge, waterflooding, well-stimulation and/or hydraulic fracturing. We have the products and know-how to condition the water, for either re-injection, disposal, discharge, or re-use.
Storage Fields
Liquid and gaseous hydrocarbon products are often stored in underground caverns, salt domes, aquifers and depleted oil fields. This clean, dry product often comes out of storage wet, and dirty and in need of filtration and separation to restore it to pipeline quality. We have the products to make that happen.
Pipeline Pigging & Waterdraw
Barrel pigs, spheres and brush pigs are routinely employed to remove corrosion products, sediment, debris, and liquids from underground pipelines. Smart pigs and hydrostatic testing are used to verify pipeline integrity. FTC has products designed to filter contaminants out of the collected liquids in compliance with industrial and environmental standards. We also offer oil-removing technology for water remediation.
Gas Separation (Coalescence)
FTC has developed a complete line of high-efficiency gas – liquid coalescers to remove the impurities below from natural gas. Our coalescer line includes models that interchange with all popular models in the field while also offering special construction for difficult site-conditions.
- Contaminants in the plant inlet gas
- Hydrocarbon condensates
- Water and brines
- Compressor lubrication oil
- Amine & glycol carry-over
- Produced water carry-over
- Completion fluids, brine, solvents & anti-foaming agents
Gas Sweetening
Amine (Lean & Rich)
FTC is very familiar with the unique requirements of gas de-sulfurization units and CO2-removal units. We have products to purify both lean and (rich solvents such as DEA, MEA, MDEA and Selexol™ to a degree of filtration efficiency that will prevent solvent foaming that leads to off-specification gas.
Flare Burner Tip Protection
Low NOx, power plant burners, and flare stacks have high flow rates, and even low concentrations of contaminants can clog burners over time. FTC can provide burner-tip protection using correct filtration products, which offer both high-efficiency and high-capacity capabilities, for prolonged trouble-free service.
Gas De-Hydration
Glycol (Lean & Rich)
Glycol units are the technology of choice to remove water from many gas streams including natural gas. FTC has products and expertise to purify TEG, DEG, TREG, MEG and protect the lean-rich heat exchangers, re-boiler fire tubes, and column packing. Our filters also assist with operators maintaining dewpoint suppression and prevent hydrate formation.
Downstream Gas Separation
Natural gas exiting these amine and glycol units often needs polishing to ensure that it is of “pipeline quality”. Upsets in contactor or absorber towers can cause carry-over of impurities into the sales gas. These can be:
- Foam residues loaded with surfactants and many other impurities
- Amine solvents
- Glycol solvents
- Hydrocarbons
Compressor Stations
Natural gas compressor stations used coalescers to protect the machinery from liquid slugging, particulate wear, hydrates, oils and pipeline debris. FTC’s filters effectively remove these contaminants.
Engine & Meter Protection
Our coalescers and dry gas filters provide protection to turbines, power plants, city gates and meter runs.
Refining
FTC has decades of experience in many refinery unit applications. Below you will find some of our areas of expertise:
Hydrotreating (Hydrodesulfurization)
Hydrotreaters use excess hydrogen gas under pressure and catalysts to remove sulfur from hydrocarbon structures. Hydrotreaters play a key role today in low sulfur emissions from gasoline and diesel. Filtration protection is critical for unit performance. Some applications are:
- Sour water
- Feed filtration
- Fuel Gas
- Catalyst bed protection
- Gas oil purification
- Catalyst recovery
Hydrocracking (HCU)
Hydrocrackers take feed streams from the crude unit and use hydrogen in a catalytic bed to hydrogenate and break large hydrocarbon molecules to smaller molecules in a controlled manner. Filtration protection is critical for unit performance. Some applications are:
- Sour water filtration
- Feed filtration
- Fuel Gas filtration and coalescing
- Catalyst bed protection against fouling
- Recycle Compressor carry-over
Catalyst Reforming (CRU)
These units combine naphtha and straight-run gasoline (SRG) to make sales ready gasoline. This unit also creates hydrogen gas, light ends and residual gas. Filtration protection is critical for unit performance. Some applications are:
- Sour water filtration
- Feed filtration
- BTEX and reformate filtration
- Hydrogen compressor protection
- Gas coalescers
- Heat exchanger protection
- Hydrogen gas purification
Sulfur Recovery Units
Amine units and Sulfur Recovery units (SRU Claus Units), remove H2S from a number of refinery gas and liquid streams. These units need to operate correctly to meet both product specifications and environmental regulations. Some filtration uses are:
- Amine rich and lean solvent filtration
- Inlet gas coalescers
- Sour water filtration
Catalytic Cracking (FCC)
Catalytic cracking takes heavy gas oil to produce diesel, naphtha, and cycle stock in addition to gasoline. In fact, the FCC unit is a very critical unit in a refinery due to its high gasoline production. Filtration protection is essential for unit performance. Some applications are:
- Sour Water filtration
- Catalyst protection
- Slurry oil purification (catalyst recovery)
- Flue gas filtration
- Boiler protection
- Gasoline purification and water separation
- Diesel purification and water separation
MTBE Production
Methyl Tert-Butyl Ether (MTBE) is an oxygenate component used in gasoline to enhance its octane. The MTBE Unit combines isobutylene and CH3OH over a fixed-bed resin catalyst. Filtration protection is critical for unit performance. Some applications are:
- Isobutylene feed
- Methanol feed
- Product MTBE filtration
Coke Removal
The bottoms of the crude distillation unit undergo thermal cracking to break large hydrocarbons (or visbreaking to lower hydrocarbon viscosity) to yield coke, asphalt and lube oils. Filtration protection is important for unit performance. Some applications are:
- Fuel gas filtration and separation
- Sour water filtration
Sour Water Stripping
Sour water strippers use steam to withdraw H2S & NH3 from various process water streams. Filtration protection is fundamental for unit performance. Some applications are:
- Sour water filtration
- Hydrocarbon removal and recovery
- Heat exchanger protection
- Corrosion solids caused by ammonia and phenols
Refined Product & Petrochemical
In tank farms and custody transfer points it is critical to keep contaminants out of the final product. All products require filtration and/or de-watering after storage. Some filtration applications are:
- Blended gasoline
- Diesel water removal
- Kerosene & jet fuel solids and water specifications
- Solvent BTEX
- Ethylene feed stocks
- Fuel oil filtration
- Bunker oil filtration
- Light ends (Butane, Pentane, Hexane, Propane, etc.)